SK Global Chemical Invests $10 Million with Closed Loop Partners to Scale Best-in-Class Plastics Recycling Solutions & Catalyze the Shift Toward a Circular Economy
July 27, 2021
With a rapidly evolving plastics industry and increasingly urgent climate challenges, SK Global Chemical joins leaders Dow, LyondellBasell & NOVA Chemicals, among others, in paving differentiated and globally sustainable ways forward for the industry
July 27, 2021, New York – Today, SK Global Chemical (SKGC) announced their investment in two of Closed Loop Partners’ funds––the Closed Loop Circular Plastics Fund and the Closed Loop Leadership Fund––to advance circular business models, scalable recycling technologies, and materials recovery infrastructure in the U.S. and Canada. Their investment will help increase the supply of high-quality recycled content to meet growing demand, return valuable materials to manufacturing supply chains and ultimately reduce extraction of virgin resources. SKGC and Closed Loop Partners’ collaboration is a critical step in demonstrating what the future of a fully circular plastics system could look like and sending a market signal to others to spur recycling markets that must mature more quickly.
“Plastics manufacturers play a key role in building circular systems for plastics––they are at the early stages of the supply chain, helping determine the quality, sustainability and recyclability of the plastics that flow through the entire system. It’s critical that these stakeholders adapt to the changing times and expectations; antiquated business models that rely on virgin plastics are no longer viable when confronted with limited natural resources and mounting plastic waste,” says Ron Gonen, Founder & CEO of Closed Loop Partners. “SK Global Chemical’s investment in our funds helps catalyze circular plastics supply chains in the U.S. and Canada, while also providing for the exchange of best practices with Asia, accelerating a circular economy at a much larger scale.”
SKGC’s investment with Closed Loop Partners builds on their ‘Zero Plastic Waste’ goals and efforts to bolster innovations across the plastics recycling system. Under their “Green For Better Life” strategy, SKGC continues to grow plastics recycling capacity globally. The company aims to recycle 900 thousand tons of plastic waste per year by 2025, lower their use of plastics, and make all of its products eco-friendly, by 2027. SKGC has formed strategic partnerships with cutting-edge advanced plastics recycling companies in North America, invested on-the-ground in new facilities that transform plastic waste into virgin-like plastics, and continues to optimize mechanical recycling infrastructure to reduce overall virgin plastic consumption. One of the reasons SKGC chose to collaborate with Closed Loop Partners is to expand its connections to a roster of leading companies working toward the circular economy, comprising both multinationals with extensive scale and emerging innovators introducing differentiated sustainable solutions. Their investment with Closed Loop Partners aligns with ambitions of their parent company, SK Innovation, to transition from “carbon to green” by investing more than $20 billion in five years.
SKGC’s investment in Closed Loop Partners’ Circular Plastics Fund, launched in May with Founding Investors Dow, LyondellBasell and NOVA Chemicals, brings the Fund closer to its goal of deploying $100 million to advance the recovery of plastics in the U.S. and Canada. The Fund’s catalytic strategy fills investment gaps to spur recycling markets, attracting additional corporate investors and financial institutions and accelerating capital inflows beyond the Fund’s own commitments. The Fund will invest in three strategic areas to increase the amount of high-quality recycled plastic available:
- Access – Increasing the collection of targeted polyethylene (PE) and polypropylene (PP) plastics by advancing current and next-generation material collection systems, including transportation, logistics and recycling sortation technologies and infrastructure.
- Optimization – Upgrading recycling systems to more efficiently aggregate, classify and sort the targeted plastics to increase the total amount of high-quality plastic, including food-grade and medical-grade plastic, sent for remanufacturing.
- Manufacturing – Investing in facilities and equipment that manufacture finished products, packaging or related goods using recycled content, including recycled PE and PP.
The Closed Loop Leadership Fund, Closed Loop Partners’ private equity arm, is a complementary market rate strategy that proves the growth and profitability of circular economy business models. The Fund acquires and scales best-in-class companies along the value chain to build circular supply chains in the U.S.––focused on extending the useful life of materials, including plastics and packaging, organics, electronics and apparel. The Fund’s value creation strategy focuses on driving resilient profitability for businesses that optimize supply chains, keep materials out of landfill and advance the circular economy.
Since its founding in 2014, Closed Loop Partners has made more than 50 investments, diverting more than 4,600 million pounds of material from landfills and back into manufacturing supply chains. The New York-based investment firm and innovation center accelerates the circular economy through a suite of solutions––including investments and research in design innovation that reduces material use and resource extraction, reuse systems that extend the useful life of valuable materials, and mechanical recycling infrastructure and advanced recycling technologies that together help recover plastics. Building on its proven track record, and extensive ecosystem of entrepreneurs, industry experts, global consumer goods companies, retailers, financial institutions and municipalities in North America, Closed Loop Partners is well positioned to form key partnerships and drive strategic investments to advance SKGC’s goals.
Na Kyung-soo, CEO of SK Global Chemical says, “We aim to build systems that keep plastics in circulation, meeting the needs of people around the world, without compromising the natural environment. Our investment with Closed Loop Partners not only helps us advance these goals, but opens doors to new strategic partnerships with leading companies that share the same vision of advancing circular systems for plastics. As a plastics manufacturer, we recognize our responsibility in transforming plastics supply chains to collect and reuse existing materials, and know that collaborating across industries is essential to system-wide impact. We look forward to working with Closed Loop Partners and their network to drive toward our shared goals.”
In accordance with SKGC’s strategic imperatives, by 2025 SKGC will invest 500 million USD to build a cutting edge advanced plastics recycling plant in Korea.
About Closed Loop Partners
Closed Loop Partners is a New York-based investment firm comprising venture capital, growth equity, private equity, project-based finance and an innovation center focused on building the circular economy. The firm has built an ecosystem that connects entrepreneurs, industry experts, global consumer goods companies, retailers, financial institutions and municipalities, bridging gaps and fostering synergies to scale the circular economy. Learn more about Closed Loop Partners here.
About the Closed Loop Circular Plastics Fund at Closed Loop Partners
The Closed Loop Circular Plastics Fund provides catalytic financing to build circular economy infrastructure and improve the recovery of polypropylene and polyethylene plastic in the U.S. & Canada, returning plastics to more sustainable manufacturing supply chains for use as feedstock for future products and packaging. Learn more about the Fund’s investment criteria and apply for funding here.
About the Closed Loop Leadership Fund at Closed Loop Partners
The Closed Loop Leadership Fund is Closed Loop Partners’ market rate private equity fund, focused on acquiring and scaling best-in-class circular business models that are fundamental to keeping plastics and packaging, food and organics, electronics and textiles out of landfills and within a circular system. Learn more about the Closed Loop Leadership Fund here.
About SK Global Chemical
In 1972, SK global chemical laid the foundation for the development of the petrochemical industry by operating the first naphtha-cracking facility in Korea. They provide various automotive & packaging products and solutions required by customers and markets, and are growing into a technology-based global chemical company through continuous R&D efforts and global expansion.
SK global chemical will achieve its vision, ‘Green for Better Life’, by establishing a plastics-based circular economy, collaborating with various partners and stakeholders. They will expand their portfolio of eco-friendly products and will continuously recycle beyond the amount of plastics that they produce, in order to realize and leverage the sustainability efforts that will benefit our planet. Learn more about SKGC here.
Disclaimer:
This publication is for informational purposes only, and nothing contained herein constitutes an offer to sell or a solicitation of an offer to buy any interest in any investment vehicle managed by Closed Loop Capital Management or any company in which Closed Loop Capital Management or its affiliates have invested. An offer or solicitation will be made only through a final private placement memorandum, subscription agreement and other related documents with respect to a particular investment opportunity and will be subject to the terms and conditions contained in such documents, including the qualifications necessary to become an investor. Closed Loop Capital Management does not utilize its website to provide investment or other advice, and nothing contained herein constitutes a comprehensive or complete statement of the matters discussed or the law relating thereto. Information provided reflects Closed Loop Capital Management’s views as of a particular time and are subject to change without notice. You should obtain relevant and specific professional advice before making any investment decision. Certain information on this Website may contain forward-looking statements, which are subject to risks and uncertainties and speak only as of the date on which they are made. The words “believe”, “expect”, “anticipate”, “optimistic”, “intend”, “aim”, “will” or similar expressions are intended to identify forward-looking statements. Closed Loop Capital Management undertakes no obligation to update publicly or revise any forward-looking statements, whether as a result of new information, future developments or otherwise. Past performance is not indicative of future results; no representation is being made that any investment or transaction will or is likely to achieve profits or losses similar to those achieved in the past, or that significant losses will be avoided.
Closed Loop Partners and ERI Enter Strategic Partnership to Strengthen Innovative Circular Economy Supply Chains
July 14, 2021
Closed Loop Partners makes a significant strategic investment in ERI; Founder & CEO Ron Gonen will join ERI’s Board
NEW YORK–(BUSINESS WIRE)–ERI, the nation’s largest fully integrated IT and electronics asset disposition provider and cybersecurity-focused hardware destruction company and Closed Loop Partners, the leading investment firm focused on building the circular economy in North America and beyond, have announced that they have entered into a partnership.
As part of the partnership, Closed Loop Partners’ Leadership Fund, part of the private equity group at Closed Loop Partners, has made a significant strategic investment in ERI. The Closed Loop Leadership Fund, established in 2019, focuses on investing in and scaling businesses fundamental to keeping packaging, organics, electronics and apparel out of landfills and within a circular system. Investors in the Fund include Microsoft, Nestlé and Unilever as well as institutional investors and family offices. Ron Gonen, Founder and CEO of Closed Loop Partners has also been elected to ERI’s board of directors.
“ERI is the leading recycler of electronics in the United States, consistently demonstrating the viability of closed loop systems for high value materials,” said Gonen. “Globally, we discard $55 billion in e-waste annually, and the waste stream is projected to grow more rapidly in the coming years, diverting these materials from landfills and back into manufacturing supply chains is critical. Our partnership with ERI will strengthen circular supply chains that ultimately benefit people, the planet and business.”
“This is the perfect time for a partnership between ERI and Closed Loop Partners,” said John Shegerian, ERI’s Chairman/CEO. “Due to a perfect storm of innovation, the internet of things, cars essentially becoming computers on wheels, an increase in wearable tech, the 4G to 5G switchover, increasing consumption, data privacy issues and other factors, e-waste is the fastest growing waste stream in the world – growing at a rate five times faster than any other waste stream. By partnering with our longtime friends at Closed Loop Partners, we are ideally positioned to play a meaningful role in accelerating change.”
“We are also honored to have Ron Gonen join our board,” added Shegerian. “It was Ron who introduced us to AMP Robotics, our partners in the development and implementation of our first-in-industry AI-driven robotic systems currently increasing operational efficiencies in our recycling facilities. He was also serving as Deputy Commissioner of Sanitation, Recycling and Sustainability for New York City when ERI teamed with the city to launch the city’s groundbreaking and award-winning residential e-waste pickup and recycling program, ecycleNYC. So there is tremendous synergy there. As a thought leader, Ron has already provided tremendous guidance and insight in terms of the circular economy and we are incredibly excited to be entering into this new level of collaboration with him and his team at Closed Loop Partners.”
About Closed Loop Partners
Closed Loop Partners is a New York-based investment firm comprised of venture capital, growth equity, private equity, project-based finance and an innovation center focused on building the circular economy. Since its founding in 2014, Closed Loop Partners’ existing portfolio of more than 50 investments has diverted more than 4,600 million pounds of material from landfills and back into manufacturing supply chains. The firm has built an ecosystem that connects entrepreneurs, industry experts, global consumer goods companies, retailers, financial institutions and municipalities, bridging gaps and fostering synergies to scale the circular economy.
About ERI
ERI is the largest fully integrated IT and electronics asset disposition provider and cybersecurity-focused hardware destruction company in the United States. ERI is certified at the highest level by all leading environmental and data security oversight organizations to de-manufacture, recycle, and refurbish every type of electronic device in an environmentally responsible manner. ERI has the capacity to process more than a billion pounds of electronic waste annually at its eight certified locations, serving every zip code in the United States. ERI’s mission is to protect people, the planet and privacy. For more information about e-waste recycling and ERI, call 1-800-ERI-DIRECT or visit https://eridirect.com.
Contacts
ERI: Paul Williams, 310/569-0023, [email protected]
Closed Loop Partners: Georgia Sherwin, 929/427-7786, [email protected]
Disclaimer:
This publication is for informational purposes only, and nothing contained herein constitutes an offer to sell or a solicitation of an offer to buy any interest in any investment vehicle managed by Closed Loop Capital Management or any company in which Closed Loop Capital Management or its affiliates have invested. An offer or solicitation will be made only through a final private placement memorandum, subscription agreement and other related documents with respect to a particular investment opportunity and will be subject to the terms and conditions contained in such documents, including the qualifications necessary to become an investor. Closed Loop Capital Management does not utilize its website to provide investment or other advice, and nothing contained herein constitutes a comprehensive or complete statement of the matters discussed or the law relating thereto. Information provided reflects Closed Loop Capital Management’s views as of a particular time and are subject to change without notice. You should obtain relevant and specific professional advice before making any investment decision. Certain information on this Website may contain forward-looking statements, which are subject to risks and uncertainties and speak only as of the date on which they are made. The words “believe”, “expect”, “anticipate”, “optimistic”, “intend”, “aim”, “will” or similar expressions are intended to identify forward-looking statements. Closed Loop Capital Management undertakes no obligation to update publicly or revise any forward-looking statements, whether as a result of new information, future developments or otherwise. Past performance is not indicative of future results; no representation is being made that any investment or transaction will or is likely to achieve profits or losses similar to those achieved in the past, or that significant losses will be avoided.
What is the Role of Plastics in the Circular Economy?
May 26, 2021
From lauded silver bullet to pariah material in just over half a century, plastic has played a complicated role in our economy. What began as an innovative material that was relatively inexpensive to produce, lightweight to transport, versatile in application and efficient in preserving goods, has resulted in 8.3 billion metric tons of plastics produced since the 1950s, half of which was produced in the past 15 years alone. Yet, while economies of scale drove down the cost to produce plastic, its costs showed up elsewhere––in the billions of tax dollars spent to send plastic to landfills, and in its degradation of our environment and communities. About 60% of plastics produced have already ended up in a landfill or the natural environment. At the rate we’re going, there could be more plastic than fish (by weight) in the ocean by 2050.
The plastics waste challenge makes clear the urgent need for us to identify a path toward a waste-free future. To achieve this ideal in the midst of today’s take-make-waste reality, a range of solutions need to be in play at the same time. To address plastic waste at every stage of the material’s life cycle––from source, to use, to end-of-life and back again––every stakeholder across the value chain must be involved. No one institution or solution can build the circular economy alone, and even if they could, change would not happen fast enough to address the urgent climate challenge. With any system-wide transformation, the path forward is complex, nuanced and involves experimentation. A collaborative, multifaceted approach can accelerate the process in a more thoughtful, holistic way.
At Closed Loop Partners, we envision a circular future for plastics. This requires building a system that reduces the need to extract virgin resources––fossil fuels––to make plastics, harnesses design innovation and material science, and champions reuse models and new product delivery models. In parallel, we must strengthen the recycling infrastructure needed to capture existing plastics after use. With over 50 investments across our funds and three pre-competitive industry consortia to solve shared material challenges, led by our Center for the Circular Economy, we act across four key pillars to advance circular plastics supply chains.
1. Scale Reusable Products and Packaging and Explore New Materials to Reduce the Need for Single-Use Plastics
Our work to build the circular economy begins at the source, by rethinking the kinds and quantities of raw materials we use, and the supply chains they flow through. Reuse, refill and resale business models keep valuable materials in play, and therefore reduce the need to extract virgin resources. At the same time, material science innovations help diversify the resources we rely on to create packaging and products. For example, organic materials, including algae, mushrooms, eucalyptus, coconut fibers and corn that are rapidly replenishable and could be composted at end-of-life, represent viable alternatives to plastics for packaging and textiles.
How do we do this?
Our Closed Loop Ventures Group invests in leading reuse and refill models, exemplified by our portfolio company, Algramo. The Chilean-based company entered the North American market in 2020, piloting their tech-enabled refill system and smart reusable packaging in New York City. Their vending machines allow customers to dispense household cleaning products by the gram, getting exactly the amount of product they need into a smart, reusable container, eliminating single-use plastic packaging. Algramo not only makes the sustainable option the most affordable alternative, but also the more accessible and convenient one.
At an even earlier stage, our innovation arm, the Center for the Circular Economy, tests emerging reusable packaging models through the NextGen Consortium and the Consortium to Reinvent the Retail Bag. In 2020, our NextGen Consortium, in partnership with Starbucks, McDonald’s and other leading foodservice brands, conducted in-market tests for new reusable hot and cold cup models at local cafes in the San Francisco Bay Area. The Consortium examined every step of the reusable cup journey: from customer sign-up, to the payment process, to cup returns. Building on our learnings, we released a report on Bringing Reusable Packaging Systems to Life, an open-source resource that highlights steps for implementing reuse models.
Our Center also researches climate-friendly material innovations like compostable packaging, as one viable solution to plastic waste when the necessary recovery systems are in place. The Center’s Compostable Packaging Consortium aims to create a decision-making framework on when to deploy compostable packaging, while building an investment roadmap to scale the composting infrastructure needed to handle these formats at their end-of-life.
2. Collaborate with Diverse Stakeholders to Accelerate Change at Scale
To move from a linear system to a circular one, every stakeholder that will be affected––including consumers, entrepreneurs, corporations, NGOs, cities, policymakers and governments––must be at the table. Creating systemic change requires collaboration across the value chain, inviting numerous perspectives and areas of expertise, and aligning on shared goals.
How do we do this?
Last year, our Center formed the Consortium to Reinvent the Retail Bag, an unprecedented multi-sector effort by leading retailers, including CVS Health, Target and Walmart, to address a common material challenge: the single-use plastic bag. Brands across the grocery, sports & outdoor goods, value, apparel & home goods sectors aligned to address shared environmental and operational challenges to move beyond short-term fixes to long-lasting, systemic solutions for how customers get their goods home. In February 2021, nine winners of the Beyond the Bag innovation challenge were selected from a pool of more than 450 innovations, and are now testing and refining solutions to improve their potential to scale.
3. Invest in Recovery Infrastructure to Recapture and Recycle Plastics, and Reduce the Need to Extract Virgin Resources
The value of plastic is not lost after a single use; keeping the material within supply chains is a matter of our economic self-interest. As corporate commitments to use post-consumer recycled materials increase, the demand for recycled plastics continues to grow, enabling a viable market. Yet, without the necessary recovery infrastructure, current supplies of recycled plastics only meet 6% of demand for the most common plastics in the U.S. and Canada. Optimizing recycling facilities and new advanced recycling technologies, among others, can increase the supply of high-quality, clean recycled material feedstocks, maximize their value over multiple lifecycles and reduce our reliance on virgin inputs dependent on the extraction of fossil fuels.
How do we do this?
Our Closed Loop Infrastructure Fund, established when the firm was founded in 2014, has helped municipalities and private companies across North America upgrade and expand their recycling infrastructure for materials––from glass, to paper and plastic. For example, the fund provided a $3 million below-market rate loan to the City of Phoenix, to upgrade its recycling facility and enable greater diversion of plastics from landfill and improve the quality of baled paper produced. This helped the city’s materials recovery facility reach its highest revenue to date in May 2020, at over $400,000, with an 18% increase in tons of residential recycled materials collected during the COVID-19 pandemic.
Our recently launched Closed Loop Circular Plastics Fund provides catalytic debt and equity financing, spurring additional mainstream investments into recycling infrastructure that can help address bottlenecks in the system for rigid and flexible polyethylene and polypropylene––plastics that need more targeted interventions to help meet their high demand in the U.S. and Canada. The commitment of stakeholders at every point of the plastics value chain is critical to evolving the plastics industry toward a more sustainable future. The founding companies invested in the fund are plastics producers and chemical companies, who have been key players in unlocking the value of resin resources through material and chemical innovations; now there is opportunity to adapt their processes to maximize the value of plastics already in circulation, championing the recovery and remanufacturing of resins to extend their useful life.
We also look to solutions that help address some of today’s most difficult-to-recycle plastics, those that cannot be processed by traditional mechanical recycling facilities. The Center’s research on advanced recycling technologies uncovers how these technologies––purification, decomposition and conversion––can help recycle many more types of plastics, expanding the scope of recoverable materials far beyond just packaging. In 2019, we conducted a landscape mapping of the technologies and opportunities, and are now conducting deeper research into the environmental impacts, policy incentives and financial case for these technologies.
4. Sustain Markets for Recycled & Climate-Friendly Materials
With the market rewarding sustainability, circularity does not mean sacrificing profits. Today, there is a market incentive to keep valuable materials within the system, instead of sending them to landfill, which costs taxpayers money and wastes $10 billion worth of materials in landfills across the United States*. Investing in companies and product innovations that incentivize the use of recycled materials or climate-friendly materials capitalizes on opportunities created by a strong, vibrant circular economy.
How do we do this?
Many of Closed Loop Partners’ portfolio companies manufacture products and packaging using recycled or new sustainable materials, proving viable, circular business models. For example, our portfolio company, AeroAggregates, produces ultra-lightweight fill material for infrastructure construction projects from 100% post-consumer recycled glass. Our Venture Group’s portfolio company, Algaeing, manufactures algae-based dyes and fibers within a zero-waste system––enabling water and energy efficiency while creating a viable alternative to petroleum-based textiles.
Our portfolio company, For Days, offers direct-to-consumer apparel made from 100% organic cotton and designed for recovery with a mail-back program. They recently launched its Closet and Credit system, which gives customers credit for returning their used clothing items. They can then use this credit toward new items sold by the company, enabling a circular zero-waste system for their clothes by turning their “closet into currency.”
To effectively build a circular economy, all of these solutions need to be in play. A successful circular economy is one where every material’s value is recognized, shared, re-used and continuously cycled. Addressing the global plastics crisis requires seeing and solving it from multiple angles; there is no panacea. We need to address today’s reality, in which billions of tons of plastics already circulate in our economy––while building for a waste-free tomorrow.
*Closed Loop Partners. Research Brief: Materials Landfilled in the United States and Opportunities to Increase Materials Recovery, 2018 Update. Closed Loop Partners Internal Research, 2019, adapted from Powell and Chertow, 2018, Powell et al., 2016, and Powell et al., 2016.
The Recycling Partnership Announces Three Grants to Improve Polypropylene Curbside Recycling for Millions of Americans
March 31, 2021
Polypropylene Recycling Coalition brings total awards to nearly $3 million in grants, impacting 7.2 million people nationally
FALLS CHURCH, Va., March 31, 2021 — The Recycling Partnership today announced a second round of grant funding through its Polypropylene Recycling Coalition, distributing nearly $1 million in catalytic grants to advance polypropylene recycling in the U.S. Launched in July 2020, the Polypropylene Recycling Coalition (Coalition) is a cross-industry collaboration supported by steering committee members Keurig Dr Pepper, Braskem, NextGen Consortium, and the Walmart Foundation, along with other members of the polypropylene value chain. Polypropylene, sometimes referred to as No. 5 plastic, is used in an array of food and non-food packaging and is in strong demand as a recycled material.
Through its second round of grant funding, the Coalition will provide an additional three grants to Materials Recovery Facilities (MRFs) across the United States to boost sortation of polypropylene and support targeted consumer education efforts. To date, the Coalition has awarded grants for seven MRFs across the U.S. These investments aim to improve curbside polypropylene recycling access for an additional 3% of all U.S. households, impacting a total of 7.2 million people nationally. This aims to increase the recovery of polypropylene by an estimated 4,300 tons annually to be made into new products, such as consumer packaging and automotive parts, rather than being sent to landfills or incineration.
“The Polypropylene Recycling Coalition is leading the effort to rapidly drive meaningful, measurable change that will improve and increase the capture of polypropylene in U.S. curbside recycling. We continue to encourage all companies that use polypropylene to join us in being part of the solution to ensure greater and better capture of this recyclable material,” said Sarah Dearman, Vice President of Circular Ventures, The Recycling Partnership. “This fast, meaningful, and collaborative work will support jobs, preserve natural resources, and help support the transition to a circular economy in the United States.”
The Coalition awards grants to MRF candidates that face significant challenges in their ability to effectively sort and recycle polypropylene. With these strategic investments, polypropylene will now be accepted curbside in more communities and sent to established end markets, encouraging the shift to a circular economy. Further supporting the shift, community members in these areas will also be educated as to what is and isn’t accepted in their curbside recycling.
The three newest grantees include:
- American Recycling in Candler, North Carolina
- DEM-CON in Shakopee, Minnesota
- Independent Texas Recyclers in Houston, Texas
The combined geographic reach of the first two rounds of grantees includes MRFs across the Northern, Southern, Eastern, and Western regions of the U.S. The widespread interest and commitment from MRFs across the U.S. to growing the collection and sortation of recyclable polypropylene clearly demonstrates the market strength for this material nationwide.
The Coalition received a strong response to both the first and second rounds of requests for proposals and continues to accept grant applications to further its efforts to advance polypropylene curbside recycling. The next grant proposal request is due June 30, 2021. MRFs interested in sorting and recycling polypropylene are encouraged to apply.
The mission-driven work of the Coalition is supported by contributions from organizations representing all segments of the material’s value chain, including the Coalition’s newest member, Sabert Corporation. In addition to the aforementioned steering committee members, other members of the Coalition include American Chemistry Council, Campbell Soup Company, Danone North America, EFS-plastics, The Kroger Co. Zero Hunger | Zero Waste Foundation, KW Plastics, LyondellBasell, Merlin Plastics, Milliken & Company, Nestlé, PolyQuest, Procter & Gamble, St. Joseph Plastics, and Winpak. The Polypropylene Recycling Coalition is advised by industry leaders including: Association of Plastic Recyclers, former EPA Administrator Carol Browner, Closed Loop Partners, Sidewalk Infrastructure Partners, Sustainable Packaging Coalition, and World Wildlife Fund.
The Coalition is part of The Recycling Partnership’s Pathway to Circularity, an initiative creating scalable solutions to packaging and system challenges to accelerate the shift to a circular economy that uses fewer finite resources.
To learn more about the Polypropylene Recycling Coalition, its members, and how to get involved in supporting its goals, visit recyclingpartnership.org/polypropylene-coalition. For MRFs interested in applying for a grant, the application is available on our website.
About The Recycling Partnership
The Recycling Partnership is the action agent transforming the U.S. residential recycling system for good. Our team operates at every level of the recycling value chain and work on the ground with thousands of communities to transform underperforming recycling programs and tackle circular economy challenges. As the leading organization in the country that engages the full recycling supply chain, from working with companies to make their packaging more circular and help them meet climate and sustainability goals, to working with government to develop policy solutions to address the systemic needs of the U.S. recycling system, The Recycling Partnership positively impacts recycling at every step in the process. Since 2014, the nonprofit change agent diverted 230 million pounds of new recyclables from landfills, saved 465 million gallons of water, avoided more than 250,000 metric tons of greenhouse gases, and drove significant reductions in targeted contamination rates. Learn more at recyclingpartnership.org
About the NextGen Consortium
The NextGen Consortium is a multi-year, global consortium that addresses single-use food packaging waste globally by advancing the design, commercialization, and recovery of food packaging alternatives. The NextGen Consortium is managed by Closed Loop Partners’ Center for the Circular Economy. Starbucks and McDonald’s are the founding partners of the Consortium, The Coca-Cola Company, Yum! Brands, Nestlé, Wendy’s and Jacobs Douwe Egberts are supporting partners. World Wildlife Fund (WWF) is the advisory partner and IDEO is the innovation partner. Learn more at www.nextgenconsortium.com.
Media Contact:
Samantha Kappalman
[email protected]
(443) 223-3322
SOURCE The Recycling Partnership
NextGen Consortium Joins the Polypropylene Recycling Coalition to Further Drive the Recovery of Plastic Packaging in the U.S.
December 08, 2020
NextGen Consortium brings its collective strength and insights to the Coalition’s Steering Committee to create stronger markets for recycled polypropylene
Dec 8 — Today, the NextGen Consortium, led by Closed Loop Partners’ Center for the Circular Economy, with Founding Partners Starbucks and McDonald’s, joined the Polypropylene Recycling Coalition as part of the Consortium’s multi-pronged approach to address single-use food packaging waste globally.
Building on the NextGen Consortium’s existing work to advance the design, commercialization and recovery of packaging alternatives — from new materials and recovery strategies to reusable packaging systems that keep materials in use for as long as possible — the Consortium will work with Coalition members to help increase recovery capacity for polypropylene in the United States. Polypropylene is typically found in everyday packaging such as the cup used for iced drinks on-the-go, yogurt cups and coffee pods, among other applications. However, in many markets, polypropylene is not accepted in residential recycling programs and ends up in landfills. According to The Recycling Partnership’s 2020 State of Curbside Recycling report, there may be as much as 1.6 billion pounds of polypropylene available per year from single-family homes that could be recycled into new products.
“Joining the Polypropylene Recycling Coalition was a natural continuation of the work we are doing across different packaging formats, systems and materials to improve the overall recovery of food packaging,” says Kate Daly, Managing Director of the Center for the Circular Economy at Closed Loop Partners. “Alongside packaging design innovation, such as growing tech-enabled reusable packaging models, capturing existing plastic packaging waste is critical for building a more sustainable future. Unrecovered polypropylene in landfills represents an untapped and wasted resource that could be recirculated in the economy, bringing value to numerous stakeholders.”
The Polypropylene Recycling Coalition, established by The Recycling Partnership, unites the industry around improving polypropylene recovery in the U.S. and further developing markets for high-quality recycled polypropylene. Today, the Coalition announced nearly $2 million in grant dollars to upgrade and improve the sorting equipment at recycling facilities and support consumer education programs to advance polypropylene recycling. The Coalition’s investments will widen the total nationwide acceptance of polypropylene in curbside recycling programs to an additional four million people, resulting in the recovery of a larger supply of polypropylene that could be made into new products.
As the NextGen Consortium continues its work across the value chain – with brands, municipalities, material recovery facilities and manufacturers – to advance viable sustainable packaging solutions that can scale throughout the global supply chain and bring value to recovery systems, working with the Polypropylene Coalition will help further our collective impact at scale.
About NextGen Consortium
The NextGen Consortium is a multi-year, global consortium that addresses single-use food packaging waste globally by advancing the design, commercialization, and recovery of food packaging alternatives. The NextGen Consortium is managed by Closed Loop Partners’ Center for the Circular Economy. Starbucks and McDonald’s are the founding partners of the Consortium, The Coca-Cola Company, Yum! Brands, Nestlé, and Wendy’s are supporting partners. The World Wildlife Fund (WWF) is the advisory partner and IDEO is the innovation partner. Learn more at www.nextgenconsortium.com.
About The Recycling Partnership
The Recycling Partnership is a national nonprofit organization that leverages corporate partner funding to transform recycling for good in states, cities, and communities nationwide. As the leading organization in the country that engages the full recycling supply chain from the corporations that manufacture products and packaging to local governments charged with recycling to industry end markets, haulers, material recovery facilities, and converters, The Recycling Partnership positively impacts recycling at every step in the process. Since 2014, the nonprofit change agent diverted 230 million pounds of new recyclables from landfills, saved 465 million gallons of water, avoided more than 250,000 metric tons of greenhouse gases, and drove significant reductions in targeted contamination rates. Learn more at recyclingpartnership.org.
Two Georgia-Pacific Recycled Paper Mills Open Opportunities for Paper Cup Recycling
September 15, 2020
ATLANTA, Sept. 15, 2020 /PRNewswire/ — Georgia-Pacific announced today that it is now accepting mixed paper bales that contain single-use polyethylene (PE)-coated paper cups at its recycled paper mills in Green Bay, Wisconsin, and Muskogee, Oklahoma. The development follows two years of partnership with the Foodservice Packaging Institute (FPI) and collaboration with the NextGen Consortium, a global initiative led by Closed Loop Partners with founding partners Starbucks and McDonald’s, to help open opportunities for paper cup recycling.
PE coatings, along with any remaining liquid and food left behind from use, have historically left single-use paper cups out of the recovery and recycling process. Georgia-Pacific, though, has proven through its extensive re-pulping trials that the Green Bay and Muskogee mills can effectively recapture valuable cup fiber from paper cups while screening out PE-coatings and reuse the fiber to make toilet tissue, napkins and paper towels.
“As single-use paper cups have grown in popularity in recent years so, too, has paper cup waste. As a leading manufacturer of paper foodservice products, we continually look for ways to consume fewer resources as part of our longer-term strategy to identify solutions that benefit society. Accepting mixed paper bales containing PE-coated cups at our Green Bay and Muskogee mills is a significant step in this direction,” said John Mulcahy, vice president of sustainability for Georgia-Pacific, which manufactures the Dixie® brand of paper cups.
Kate Daly, managing director of the Center for the Circular Economy at Closed Loop Partners, believes Georgia-Pacific’s new repulping capability will greatly benefit the foodservice industry and further advance the industry’s environmental stewardship. “We are heartened to see Georgia-Pacific accelerate paper cup recycling through its acceptance of cups in mixed paper bales. This acceptance will also benefit new non-polyethylene next generation cups, marking an important step forward for the industry as a whole, and we hope even more mills will follow this lead. Georgia-Pacific’s actions reinforce the value of the materials in paper cups and build critical markets for recycled materials. As the managing partner of the NextGen Consortium, we continue to work with leaders like Georgia-Pacific to engage, educate, and collaborate with stakeholders across the cup value chain in order to keep valuable materials in play,” she said.
Beyond its current repulping efforts, Georgia-Pacific is also collaborating with the NextGen Consortium to trial at its mills next generation paper cups that have replaced the PE-coating with materials that can be recycled and/or composted. As founding partners of the NextGen Consortium and strong advocates of reducing single-use paper cup waste, McDonald’s and Starbucks are supportive of ongoing collaboration with Georgia-Pacific and encouraged by the company’s current re-repulping efforts.
“Increasing and improving the recyclability of cups is a vital part of our work within the NextGen Consortium. We are taking a meaningful step forward with Georgia-Pacific toward our goal of reducing paper cup waste. We’re excited by this progress and look forward to our continued partnership with organizations that support our vision of a resource-positive future,” said Michael Kobori, chief sustainability officer at Starbucks.
Marion Gross, chief supply chain officer, North America with McDonald’s added, “Recovering, recycling, and reusing the valuable materials in our cups is an important part of our sustainability ambition and our work with the NextGen Consortium. By accepting and reprocessing single-use cups, Georgia-Pacific is not only enhancing recycling pathways but also generating a supply pipeline of recycled content critical to positively impacting the environment and achieving our goals.”
With its Green Bay and Muskogee mills now engaged, Georgia-Pacific is working with FPI to expand and accelerate single-use PE-coated paper cup acceptance in curbside recycling programs in an effort to increase the number of households that can recycle the paper cups. As the voice of the foodservice packaging industry, FPI is committed to reducing the impact of its products on the environment and to advancing recycling and composting. “We are thrilled to work with Georgia-Pacific in its effort to recover and reuse PE-coated paper cups, and we are excited to partner with new communities that previously didn’t have the capability to recycle them,” said Natha Dempsey, president of FPI.
About Foodservice Packaging Institute
Founded in 1933, the Foodservice Packaging Institute is the trade association for the foodservice packaging industry in North America. FPI promotes the value and benefits of foodservice packaging and serves as the industry’s leading authority to educate and influence stakeholders. Members include raw material and machinery suppliers, manufacturers, distributors and purchasers of foodservice packaging. For more information or to follow us on social media, visit www.fpi.org.
About NextGen Consortium
The NextGen Consortium is a multi-year, global consortium that addresses single-use food packaging waste globally by advancing the design, commercialization, and recovery of food packaging alternatives. The NextGen Consortium is managed by Closed Loop Partners’ Center for the Circular Economy. Starbucks and McDonald’s are the founding partners of the Consortium, The Coca-Cola Company, Yum! Brands, Nestlé, and Wendy’s are supporting partners. The World Wildlife Fund (WWF) is the advisory partner and IDEO is the innovation partner. Learn more at www.nextgenconsortium.com.
About Georgia-Pacific
Based in Atlanta, Georgia-Pacific and its subsidiaries are among the world’s leading manufacturers and marketers of bath tissue, paper towels and napkins, tableware, paper-based packaging, cellulose, specialty fibers, nonwoven fabrics, building products and related chemicals. Our familiar consumer brands include Quilted Northern®, Angel Soft®, Brawny®, Dixie®, enMotion®, Sparkle®, Mardi Gras® and Vanity Fair®. Georgia-Pacific has long been a leading supplier of building products to lumber and building materials dealers and large do-it-yourself warehouse retailers. Its Georgia-Pacific Recycling subsidiary is among the world’s largest recyclers of paper, metal and plastics. The company operates more than 150 facilities and employs more than 30,000 people directly and creates approximately 89,000 jobs indirectly. For more information, visit: gp.com.
SOURCE Georgia-Pacific
Related Links
http://www.gp.com
Closed Loop Partners at the United States Senate Environment and Public Works Committee on Recycling
June 19, 2020
Launched in 2014, Closed Loop Partners (CLP) is the first investment firm primarily focused on building the circular economy. Our vision is to help build a new economic model focused on a profitable and sustainable future that aligns the interests of shareholders, brands and local communities and the environment that we all share. Closed Loop Partners provides equity and project finance to scale products, services and infrastructure at the forefront of the development of a circular economy. We have over the past 5 years built a development system that connects entrepreneurs, industry experts, global consumer goods companies, retailers, financial institutions and municipalities.
On June 17, 2020, Bridget Croke, Managing Director, at Closed Loop Partners spoke at the United States Senate Environment and Public Works Committee as they held a hearing on “Responding to the Challenges Facing Recycling in the United States.” The following text is drawn from her testimony.
Today, we have over 40 investments in companies and municipal projects in the United States, all focused on helping Americans avoid landfill disposal fees while generating good jobs in the recycling and manufacturing sector. Our investors are a combination of some of the largest American based consumer brands in the world including 3M, Coca-Cola, Colgate Palmolive, Johnson & Johnson, Keurig Dr. Pepper, PepsiCo, Procter & Gamble, Unilever and The Walmart Foundation, as well as the American Beverage Association, institutional investors, family offices and environmental foundations. CLP proves that public–private partnerships are critical to unlocking the capital needed to build robust recycling and circular economy infrastructure needed to create jobs, reduce waste and build the supply chains of the future.
Despite some of the headlines we’ve all seen, recycling is big business in America and should create the manufacturing feedstock for future packaging. In 2019, the recycling industry in America generated over $110 billion in economic activity, $13 billion in federal, state, and local tax revenue and 530,000 jobs. In spite of COVID and market challenges in recent years, 2020 is shaping up to be a year of major innovations in the recycling industry as it becomes central to circular economy business models that major consumer goods companies and cities are deploying. Transitioning US manufacturing to circular supply chains could unlock a $2 trillion opportunity.
Recycling continues to be the most cost-effective option for the vast majority of American cities. The economics are simple. Cities have two choices when it comes to disposal: recycle or landfill. While the value of recycling is generally reported as the amount that a city can be paid for its recyclables, the core economic value of recycling is actually the opportunity for a city to avoid costly landfill disposal fees. Economic analysis conducted has shown that the U.S. scrap recycling industry is a major economic engine powerful enough to create 531,510 jobs and generate $12.9B in tax revenue for governments across the US.
New York City, the largest market in the United States, is an example of how advanced recycling infrastructure and strong local markets create long term profits. New York City has a long-term public-private partnership with Pratt Industries that converts all of its recycled paper locally into new paper products sold back into the NYC market. Via its contract with Pratt, New York City is paid for every ton of paper its residents recycle, as opposed to a cost of over $100 per ton to send paper, plastics and metals to a landfill.
Minneapolis is another good example. Eureka Recycling and the City of Minneapolis invested in local community outreach focused on keeping their recycling stream clean of contamination, defined as non-recyclable material. The result is one of the lowest contamination rates of any municipal recycling program in the country. With a clean stream of valuable recyclables, Eureka consistently shares with Minneapolis the profits earned from the sale of their recyclables. In many other cities, unfortunately, approximately 15% of the material that arrives at the municipal recycling facility is considered contamination. Municipal recycling programs that keep contaminants out of the recycling stream via strong community outreach or enforcement realize lower costs and better revenue opportunities. Municipalities that recognize that recycling is part of the commodities industry, not the waste industry, generate value.
Along with the examples of Pratt Industries in New York City and Eureka Recycling in Minneapolis, Recology in San Francisco and Balcones in Austin, among others, continue to provide their municipal and commercial customers robust recycling service. In addition, municipalities like Pensacola, Florida and Davenport, Iowa that manage their own best in class recycling facilities consistently reduce landfill disposal costs and create local economic value for their constituents.
The value of recyclable commodities continues to have a wide range. The cost to process municipal recyclables at a recycling facility is, on average, $70 per ton. That means that for a recyclable commodity to have value, it must have a market that pays the recycling facility over $70 per ton of that material. A sample of the commodities that are usually profitable to recycle include PET plastic (beverage containers), HPDE plastic (laundry detergent and soap containers), rigid polypropylene (bottle caps, some yogurt containers), cardboard and aluminum.
In 2020, three innovations are driving the increased profit potential of recycling in America and the development of a vibrant and growing Circular Economy.
- The introduction of robotics and artificial intelligence. The future of the industry will be led by the recycling facilities that produce the highest quality commodity bales of materials. Companies like AMP Robotics have introduced robotics (robots) with artificial intelligence systems that enable the sorting and production of high-quality commodity bales, supply chain tracking and safeguards against contamination that were never before imagined in the industry.
- Packaging innovation. We are seeing the emergence and growth of smart refillable packaging systems like Algramo that makes it cheaper and more convenient for consumers to use packaging more than one time. We are also seeing a growth in packaging that is designed to be recycled for value. Temperpack, for example, is a packaging technology that uses recycled cardboard to keep packaged food cold, replacing a significant amount of low value plastics like Styrofoam peanuts, which are both not recyclable and a common contaminant in the recycling system.
- Advanced plastics recycling technologies, including purification technologies and chemical recycling technologies. Purification is an enzymatic process that improves the quality of recycled plastics so they can more easily be used again in packaging. P&G invented a technology and helped launch a company, PureCycle Technologies, that will significantly increase the value of recycled plastic by removing color and smells. Chemical recycling is a process whereby plastic is depolymerized back to the base monomer, intermediary or carbon state in order to remanufacture a new plastic. Some plastics, like PET, HDPE and rigid polypropylene have significant value and are very profitable for the recycling industry, but they can degrade after a number of recycling cycles while some other plastics currently have limited value or are challenging to recycle. Chemical recycling has the potential to create an infinite circular economy value loop for all plastics. Some of the leading innovators are backed by major consumer goods companies. In 2020, we expect a number of emerging companies to move from pilot to commercialization phase.
These and other circular advancements are attracting significant private capital from leading investors. The industry saw investments from leading investors across asset classes. Google and Sequoia invested in AMP Robotics, Goldman Sachs is now the largest shareholder in Lakeshore Recycling Systems, Citi is largest investor in rPlanet Earth, a bottle-to-bottle plastics recycling facility in California and SJF Ventures invested in TemperPack.
The emerging leadership demonstrated by a number of retailers and consumer brands is driving the growth of the circular economy and improvements in recycling. Leadership means designing products and packaging that are free of any non-recyclable material and profitable for recycling. These packages are manufactured with recycled content, while reducing raw material inputs. Brands are telling their consumers that their commitment is to use recycled content in their packaging. Leaders are transparent in their progress, reporting in their annual reports the use of different recycled feedstocks. They know that any product or package that is not recyclable is destined for a landfill (or even worse, a river or ocean), and that cost is passed to the taxpayer.
Walmart has developed design for recycling guidelines for their suppliers to ensure the products sold in their stores are recyclable and piloting refillable packaging models. Unilever’s Seventh Generation Brand uses mostly recycled HDPE plastic in its packaging and recycled paper in its paper products. And over 10 global companies have invested over $150m in CLP’s investment funds so together we can help spur more innovation and create more tons of recycled feedstock coming through systems in the US.
We are also seeing a major trend amongst consumer goods companies looking to increase their use of recyclable material in the packaging and products they sell. It makes sense. At scale, along with the considerable environmental benefits, it should be less expensive for companies to manufacture using recycled material. That is why most major beverage companies including Coca-Cola, Keurig Dr. Pepper, PepsiCo, Nestle and Danone as well as the world’s largest consumer goods companies such as P&G, Unilever and Colgate Palmolive are publicly communicating aggressive goals for the use of recycled materials in their products and packaging.
For Americans, recycling is a matter of economic self-interest. Recycling our cardboard, paper, beverage bottles, rigid plastics containers, and aluminum cans has three important outcomes. First, it reduces the cost to manufacture the products we buy. Second, it reduces the amount of our taxpayer dollars used every year to pay landfills. Third, it generates revenue for our communities via the sale of recyclable commodities. A recent analysis reported the average cost to dispose of a ton of municipal waste in the US in 2019 was $55 per ton, and disposal fees in some states average more than $100 per ton.
Despite these economic incentives, large parts of the United States still have little or no recycling collection or processing infrastructure. Much of the economic activity generated by recycling is accomplished by long standing recycling programs on the West and East Coast as well as the upper Mid-West of America. For those who live in parts of the country with limited or no recycling infrastructure, their tax dollars are wasted on the cost of sending valuable commodities to landfill that could otherwise be sold. While the 90m tons currently recycled in the United States saves American taxpayers and businesses over $3 billion annually in landfill disposal fees, over 180 million tons of recyclable materials are landfilled, costing American taxpayers and businesses over $5 billion annually in landfills fees. We are literally throwing money in the garbage.
It is also important to recognize how China, which has received much press as of late for their role in the American recycling ecosystem, impacts the industry. For much of the past 20 years, the U.S. recycling industry was dependent on China as the leading export market. As consumption and waste has increased in China, the Chinese government has decided to develop their own domestic recycling infrastructure. This may cause some short-term pain in some parts of the United States’ recycling industry, but leading companies in the recycling industry, consumer goods and packaging industry, as well as a number of investors, see this as an opportunity to further develop and profit from domestic recycling and manufacturing infrastructure.
These are exciting times in the recycling industry as the development of the circular economy continues to expand. Major innovations are entering the industry ranging from robotics to supply chain mapping to advanced technologies that recycle plastics. Like any major industry analysis in the U.S., there is no one or two cities that should be extrapolated to define the industry. There are cities where recycling is profitable and a major economic engine and there are cities where the recycling program is struggling. What is clear is that the cities that focus on limiting contamination in their recycling program, build efficient and effective material recovery facilities and who contract with best in class recycling companies benefit from recycling programs that are both profitable and produce good local jobs.
Leading municipalities, recyclers, manufactures and brands are starting to partner together to establish, and profit from, a circular economy in the United States where goods are continually manufactured using recycled material from local recycling programs. This partnership in developing a circular economy will result in one of the largest investment opportunities in the United States over the next decade, major reduction in landfill disposal fee paid by municipalities, and become a primary driver of job creation in local economies.
We encourage policy makers to build incentives and develop policy to spur the market for recycled content and product and system innovation that reduces waste, creates jobs and makes recycled content competitive with the raw material market.
Closed Loop Partners Invests $2 Million in Reterra to Further Close the Loop on PET Plastic & Keep Valuable Materials in Play
March 03, 2020
Using advanced recycling technologies, Reterra turns discards from the plastic recycling process into high-value intermediary products.
NEW YORK, March 3 — Today, Closed Loop Partners announces a $2 million investment in Reterra, a Houston-based advanced recycling company founded in 1999. Reterra’s technology turns waste byproduct streams of PET plastic that are produced during the recycling process into high value intermediary products. In doing so, Reterra creates a market for material that would otherwise typically end up in a landfill, while also improving the overall economics of PET recycling.
With 3-6% of material lost throughout the recycling process of PET, and the demand for recycled plastic set to grow, there is a significant and growing opportunity for recapturing the discarded material from PET recyclers. Thirty seven of the world’s largest brands and retailers have made public commitments to incorporate a specified amount of recycled content in their packaging within the next ten years. This demand creates the pull through the recycling system and sends signals to packaging suppliers and manufacturers to shift their supply chains in order to include more recycled content.
“Reterra’s advanced process serves a critical role in lowering the cost of PET recycling by capturing even the smallest discards of material and making a high value product from them. This solves a system-wide issue that will become increasingly important as the market for recycled plastics continues to grow,”
Ron Gonen, CEO of Closed Loop Partners.
Reterra’s innovative technology transforms the discards into a liquid intermediary that becomes useful feedstock for a number of different applications, thus turning waste into value. The investment from Closed Loop Partners will help finance the move into their recently-acquired new facility and upgrade equipment to increase capacity and meet new customer demands. The new plant will double capacity immediately, enabling them to increase processing to almost 100 million pounds of material annually within two years.
“For the last five years we’ve been operating at capacity, but with the help of Closed Loop Partners we are now able to take our business to the next level and capitalize on the growing market demand for our products,”
Jason Ball, President of Reterra.
The investment comes via Closed Loop Partners’ Infrastructure Fund, its first project finance fund. The fund is backed by the world’s largest brands and retailers and aims to build recycling and circular economy infrastructure across the United States to better recapture materials and get them back into manufacturing supply chains.
About Closed Loop Partners
Closed Loop Partners is a New York based investment firm comprised of venture capital, growth equity, private equity, project finance and an innovation center. The firm invests in the circular economy, a new economic model focused on a profitable and sustainable future. Investors include many of the world’s largest consumer goods companies and family offices interested in investments that provide strong financial returns and tangible social impact.
Media contact: [email protected]
America’s Leading Beverage Companies Unite To Reduce New Plastic Use & Increase Collection Of Their Valuable Bottles Through ‘Every Bottle Back’ Initiative
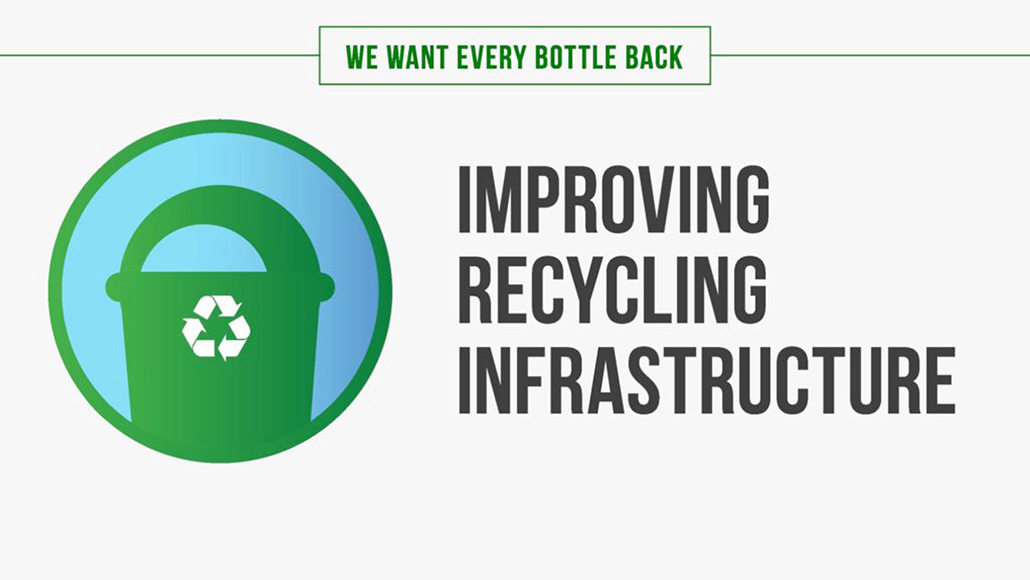
The Coca-Cola Company, PepsiCo and Keurig Dr Pepper Will Support Circular Plastics Economy Through Investment and Action, in Conjunction with World Wildlife Fund, The Recycling Partnership & Closed Loop Partners
WASHINGTON – America’s leading beverage companies – The Coca-Cola Company, PepsiCo and Keurig Dr Pepper – today announced the launch of the Every Bottle Back initiative, a breakthrough effort to reduce the industry’s use of new plastic by making significant investments to improve the collection of the industry’s valuable plastic bottles so they can be made into new bottles. These competitors are coming together to support the circular plastics economy by reinforcing to consumers the value of their 100% recyclable plastic bottles and caps and ensuring they don’t end up as waste in oceans, rivers or landfills. This program is being executed in conjunction with two of the country’s most prominent environmental nonprofits and the leading investment firm focused on the development of the circular economy. The World Wildlife Fund (WWF) will provide strategic scientific advice to help measure the industry’s progress in reducing its plastic footprint and The Recycling Partnership and Closed Loop Partners will assist in deploying funds for the initiative.
“Our industry recognizes the serious need to reduce new plastic in our environment, and we want to do our part to lead with innovative solutions. Our bottles are designed to be remade, and that is why this program is so important. We are excited to partner with the leading environmental and recycling organizations to build a circular system for the production, use, recovery and remaking of our bottles. Every Bottle Back will ensure that our plastic bottles are recovered after use and remade into new bottles, so we can reduce the amount of new plastic used to bring our beverages to market. This is an important step for our industry, and it builds on our ongoing commitment to protecting the environment for generations to come.”
Katherine Lugar, president and CEO of the American Beverage Association (ABA)
The Every Bottle Back initiative, spearheaded by ABA, will:
- Measure industry progress in reducing the use of new plastic in the United States through a collaboration with ReSource: Plastic, WWF’s corporate activation hub to help companies turn their ambitious plastic waste commitments into meaningful and measurable progress by rethinking the way plastic material is produced, used and recycled. Specifically, ABA will use the ReSource: Plastic accounting methodology to track on the collective progress made on executing strategies to reduce the use of new plastic as well as a resource in identifying additional interventions.
- Improve the quality and availability of recycled plastic in key regions of the country by directing the equivalent of $400 million to The Recycling Partnership and Closed Loop Partners through a new $100 million industry fund that will be matched three-to-one by other grants and investors. The investments will be used to improve sorting, processing and collection in areas with the biggest infrastructure gaps to help increase the amount of recycled plastic available to be remade into beverage bottles.
- Launch a public awareness campaign to help consumers understand the value of 100% recyclable bottles through community outreach and partner engagement and reinforce the importance of getting these bottles back, so they can be remade into new bottles. According to a poll conducted by Public Opinion Strategies (POS) on behalf of ABA, nearly half of consumers were unaware that America’s leading beverage companies are already making bottles that are 100% recyclable, including the caps.
- Work together to leverage our packaging to remind consumers that our bottles are 100% recyclable and can be remade into new bottles. Beverage companies will begin introducing voluntary messaging on packages beginning in late 2020.
“Reaching our goal of No Plastic in Nature by 2030 will only happen if business, governments and the NGO community work together to fix a broken plastic material system. ABA is driving this sense of collaboration within the beverage industry to address one critical piece within this system, which is PET recycling in the U.S. Measured by our ReSource: Plastic footprint tracker, the efforts made through Every Bottle Back will be met with data-driven solutions to ensure that real progress is being made. We hope the ambition raised by this initiative will inspire other industries to follow suit within the broader effort to stop plastic waste pollution.”
Sheila Bonini, senior vice president of private sector engagement at WWF
“The beverage industry cannot deliver on its promises of sustainable packaging without serious improvements to the current U.S. recycling system. Working in partnership with the beverage industry on its Every Bottle Back initiative will help to improve local recycling and provide Americans with stronger recycling programs for all materials, including plastic bottles. We applaud ABA’s members for launching meaningful, measurable work.”
Keefe Harrison, chief executive officer of The Recycling Partnership
“The leadership exhibited by The Coca-Cola Company, PepsiCo and Keurig Dr Pepper provides the investment necessary to optimize recycling in these cities and states. This partnership will serve as a model for the effectiveness of industry collaboration in modernizing recycling infrastructure and driving a reduction in the use of virgin plastic.”
Ron Gonen, chief executive officer of Closed Loop Partners
The majority of plastic beverage containers in the United States are made from polyethylene terephthalate, or PET, a strong, lightweight and safe plastic approved by the U.S. Food and Drug Administration (FDA) for use in food and beverage containers. It is unique, and because of its quality and versatility, recycled PET for years has been in high demand for use in an array of products as varied as clothing, carpets and playground equipment. Through the Every Bottle Back initiative, beverage companies are stepping up efforts to reclaim as much plastic packaging as possible to ensure it is remade into new PET bottles.
These efforts support other sustainability efforts underway by The Coca-Cola Company, PepsiCo and Keurig Dr Pepper.
“We’re proud to come together with our competitors to address the serious issue of plastic waste in our environment. We know we cannot do this alone and, in order to meet our goals and those of our industry, we need to work in partnership to drive collective action to ensure our bottles have second, third and fourth lives through continued recycling and re-use.”
James Dinkins, president, Coca-Cola North America
“At PepsiCo, we are striving to build a world where plastics need never become waste. We are proud to collaborate with others in the industry and respected partners to advance that vision and to do the hard work needed to educate consumers, enable collections and inspire action to recycle our plastic bottles. More recycled plastic lessens the need for new plastic.”
Kirk Tanner, chief executive officer, PepsiCo Beverages North America
“We have seen the meaningful impact this industry can have when we collaborate, and we are proud to be partnering to reduce our collective use of new plastic, while increasing the recycling and reuse of our 100% recyclable bottles. The Every Bottle Back initiative supports KDP’s top environmental priority to reduce packaging waste, as we work to support a circular economy with strong collective action.”
Derek Hopkins, chief commercial officer, Keurig Dr Pepper
Learn more about the Every Bottle Back initiative at www.EveryBottleBack.org. To schedule an interview, please contact the ABA press office at [email protected].
The Latest Insights and Analysis from Chris Cui, Director of Asia Programs
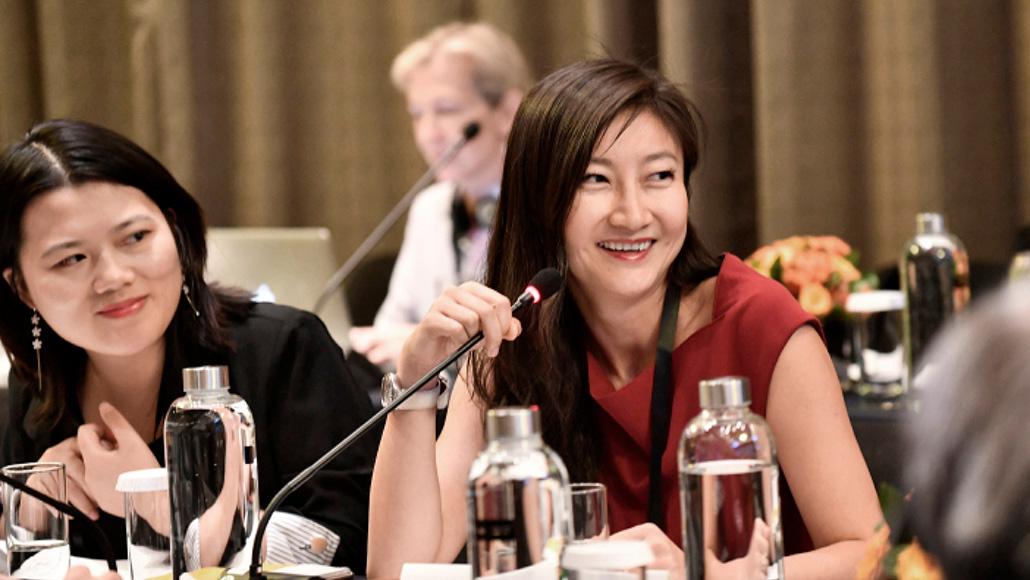
The revision of China’s Solid Waste Management and Pollution Prevention Law could have far reaching impact on brands and recyclers.
A proposed revision to the Solid Waste Management and Pollution Prevention Law in China could affect the operations of brands and recyclers. The revised law entered the review phase at the 13th National Congress on June 25, 2019 and is now seeking public opinion. Below are some key implications of the clauses:
Impact on the packaging industry
Clause 2.13: Companies that produce, use, and store solid waste (SW) should publish their waste management information. Publicly listed companies must also publish their preventive measures against SW pollution.
This represents a significant departure from current protocol. Increased transparency and mandatory reporting requirements for public companies will incentivize companies to invest in SW prevention, potentially providing reputational rewards to those best-in-class. This kind of impact oriented investment fits nicely with the growing interest in ESG investing in China.
Clause 3.20: Producers of SW must pay Environmental Protection Tax.
This would add a new expense for manufacturers that could be passed onto consumers too. The commercial real estate sector in China recently had to adjust to the introduction of this, where previously they did not have to worry about their waste management expenses.
Clause 3.21: The design and production of packaging must follow green production standards that will be set up by the State Market Regulation to reduce waste generation. Producers of materials that fall under mandatory recycling categories must be responsible for the recycling of their materials. The list of mandatory recycling materials will be produced by NDRC (National Development and Reform Committee).
Clause 3.22: The government will encourage R&D institutes and producers to develop and use materials that can be easily recycled, safely stored, and that can decompose in a natural environment. Packaging materials that can’t be easily composted will be banned.
Clause 3.21 and 3.22: It’s encouraging to see that the government is not only promoting recycling, but also the reduction of waste through circular design and materials innovation. This will force brands to adopt circular packaging principles, so there will be a lot of room for innovation in eco-friendly packaging.
Clause 3.42: There will be EPR for electric appliances and other products.
Since 2018, this kind of EPR has been in effect for electric vehicle manufacturers, requiring better lifecycle management across the value chain – from product design and consumption to the recycling and waste management related to electronic vehicles at end-of-use.
Impact on the recycling industry:
Clause 3.28: Permits must be required for the transportation of SW across cities.
Demand for distributed, modular recycling units will grow so that waste can be processed more locally. The need for smart logistics will grow in tandem to optimize for more efficient transportation routes, among other things.
Clause 3.29: There should be a complete solid waste import ban by 2020.
While there has been a lot of speculation in the U.S. regarding whether or not China will implement a total waste import ban by late 2020, as declared in 2017, it is clear that the Chinese government plans to move ahead with this.
Clause 3.57: There will be differential charging schemes for residential waste.
The mandatory sorting of residential waste was introduced in certain pilot cities in China on July 1, 2019. In a district in Shanghai, it now costs $17 USD to dispose of 120 liters of food waste. You can read more about this on our blog on Recycling Rises to Power in China.
Although we do not know how likely it is that all of the proposed revisions will pass or when, the fact that there are so many proposed changes to the current law, which came into force in 1995, and that they’ve gone all the way to the desk of the National Congress, is a signal that waste management is a high priority for the central government. By reviewing the proposed changes, companies in China and abroad can better prepare for what’s coming down the line.
Unlike Europe, where the circular economy is championed by investors, the government, and consumers, in China it’s the government taking the driver’s seat. The proposed revisions to the law illustrate the steps the government is willing to take to develop the circular economy in China. In turn, industries are taking note and are seizing the subsequent business opportunities.
I would encourage brands that consider China as one of their key markets to give serious thought on how they can create a circular advantage to meet the growing demand for sustainable products in China before their competitors do. This will be critical in a context where a country is implementing increasingly strict solid waste management laws.
The reform on plastic pollution in China, the next big thing after National Sword?
At the 10th meeting of the Central Committee for Deepening Overall Reform on September 9th, chaired by the Chinese President, plastic waste reform was listed as a key issue. The following was cited:
“Actively responding to plastic pollution by restricting the production, sale, and use of some plastic products, actively promoting recyclable and biodegradable substitute products, and regulating plastic waste.”
We are still waiting for a detailed reform plan, but this is another huge boost for the development of a circular economy in China, supported by the government. Brands and recyclers in China and overseas should start to prepare for the changes brought by a reform like this.
The Key Takeaways from Fortune’s First Global Sustainability Forum:
This September, in Yunnan, China, I attended Fortune’s first Global Sustainability Forum, speaking on a panel on Waste Not. The Forum dived deep into the business opportunities and challenges that arise from the transition from a linear to circular economy, highlighting the following key points:
- There are three key driving forces behind circularity: increasing shareholder activism and interest in public companies’ ESG commitments; public awareness among consumers on the environmental footprint of products and services; and growing regulation in Europe and Asia to tackle waste issues, especially plastic pollution.
- Finance is slowly but surely reckoning with the economic risks posed by climate change and other environmental threats. ICBC, the world’s largest bank by assets, ran a stress test in 2015 and, we learned, issues higher interest loans to firms that are over-exposed to environmental hazards. The stress tests began in 2015, and have changed the way Chinese banks look at the businesses they fund, now reducing their exposure to coal projects and increasing their exposure to renewable energy.
- Building sustainable supply chains is challenging due to limited transparency around data, a lack of focused financing, and water and waste management typically being too cheap to account for negative externalities. Labor specific issues also often take precedence.