3 Reasons Why Recycling is Good Business in America and a Key Driver of the Circular Economy
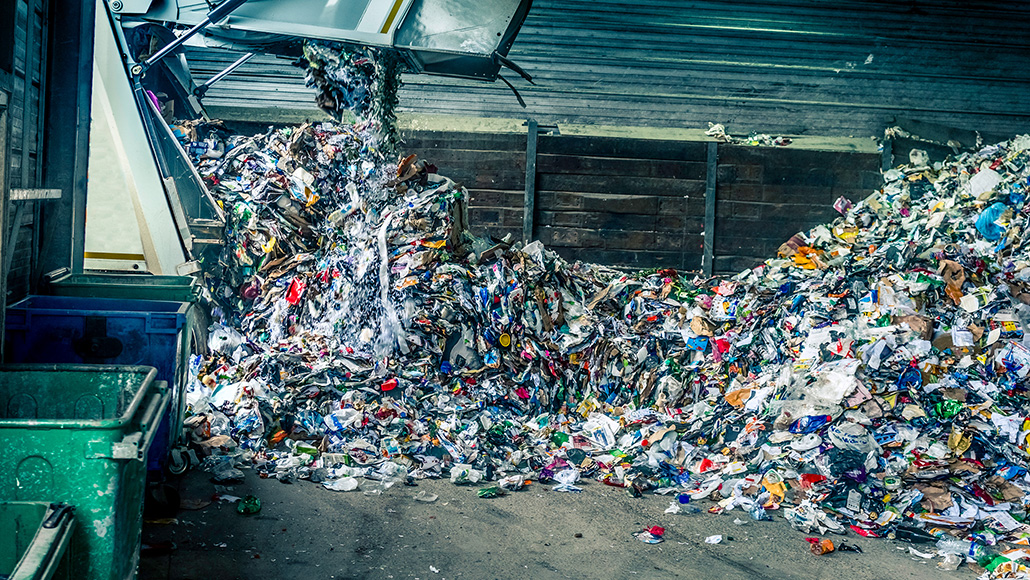
It’s Earth Day 2019 and it’s time to celebrate one of our best traditions: recycling. There’s a lot happening in our industry today: from new robots that sort recyclables to technologies transforming recycled plastics into valuable commodities. Other big themes to celebrate: opportunity and profit.
Last year, Closed Loop Partners, and firms that co-invested with us including Goldman Sachs, Citi, Google and Engie, invested over $210 million dollars in companies that are building a circular economy. The world’s largest consumer goods companies are on board too, many making public commitments to use recycled content ratios of up to 50% in their products.
Why? Because they see opportunity – and value. Natural resource extraction is expensive and landfills are unsustainable. As we shift towards a regenerative, circular economy and unlock the embodied $1 trillion value, we know that recycling is a crucial piece of the puzzle.
Today of all days, let’s take a minute to appreciate the true value of recycling in America – and let’s commit to keep going. Here’s what you need to know to celebrate recycling when talking to friends, family, and colleagues:
Recycling is Profitable: It’s good for taxpayers, municipalities, manufacturers, and investors
The recycling industry is an economic engine, providing over 500,000 jobs in America and creating more than $100 billion in revenue. The metal, paper, plastics, electronics, textiles and glass in the recycling stream are inherently valuable. While commodity markets do fluctuate, most of our waste still commands high prices, especially materials like PET, used in water bottles, which sold for $309 per ton, or clear HDPE, used in milk jugs, for $734 per ton, on average in 2018. Let’s think about the alternatives. If these materials end up in landfills, it’s taxpayers’ money that foots the bill. With a national average disposal cost of more than $50/ton, communities would have to pay over $3 billion annually in additional landfill disposal fees if these materials weren’t recycled.
Case in Point: Lakeshore Recycling Systems (LRS), Illinois. LRS serves greater Chicago and Northern Illinois, providing residential and commercial collection of recyclables, single stream recycling and construction and demolition processing services. LRS has been so successful in the past 5 years that Goldman Sachs is now their biggest investor. In their Heartland facility in 2018, they achieved revenues of approximately $65/ton and now they employ over 150 people. This best in class operation is the manufacturing feedstock for circular supply chains.
Recycling Reduces Costs & Volatility: That’s good for business
With scarce resources and increasingly volatile markets, many of the world’s largest corporations are shifting toward circular supply chains that are stable, protect the environment and reduce costs. In doing so, they avoid the volatile extraction costs embedded in manufacturing materials, like plastic. The demand for recycled materials is growing.
Case in Point: Public commitments by 37 major corporations. Thirty-seven of the world’s largest consumer brands and retailers, including Coca-Cola, Danone, Nestlé, PepsiCo, Unilever, Walmart, and others have made public commitments to use recycled plastics in their packaging within the next 10 years. Current projections indicate new real demand in North America of 5 million to 7.5 million metric tons annually by 2030. Even better? There are technologies transforming plastics waste into the building blocks for new materials that are ready to meet this demand. As these scale, a potential revenue opportunity of $120 billion in the U.S. and Canada awaits.
The Industry is Growing Here at Home: The opportunities are endless
When China stopped importing foreign scrap, the recycling industry was shaken. Business as usual no longer sufficed. But this wasn’t an end to the industry, it was a wake-up call. It pushed us to invest in domestic infrastructure, process our own waste and deliver higher quality bales of recycled materials. Materials Recovery Facilities (MRFs) that were already doing this, like Eureka Recycling in Minnesota, were less vulnerable to China’s bans. The residual contamination rates of their operations are less than 8 percent and 90 percent of their recovered material goes to markets in the state, supporting regional growth. MRFs are now identifying opportunities to up their game and invest in new equipment and technologies to enhance their performance. Innovative companies like AMP Robotics are gaining traction; they use AI and robotic arms to effectively sort materials. More and more investment opportunities are materializing. Global companies like Nine Dragons, one of the largest paper manufacturers in China, are now investing hundreds of millions of dollars on recycling infrastructure in the US.
Case in Point: Pratt Industries, Georgia. Pratt Industries is the world’s largest, privately-held 100% recycled paper and packaging company, headquartered in Georgia. This year they’re opening a new paper mill outside of Columbus, Ohio, and also opened a paper mill in Indiana. They’ve also relocated some of their MRFs to larger facilities to accommodate high demand and have pledged to invest $2 billion in the company’s U.S corrugated box manufacturing. Pratt Industries also pays New York City for all of its recycled paper and cardboard in order to meet restaurants’ demand for pizza boxes made from these recycled materials. The City of New York generates revenue of approximately $15/ton for cardboard while reducing waste, landfill costs, and greenhouse gas emissions.
Our message this Earth Day? Keep recycling as a simple way to support a circular economy.
It’s good for the planet, it’s good for cities, and it’s good for business.
Learn more at: www.closedlooppartners.com
We Can Accelerate Solutions for Plastics & Circular Supply Chains
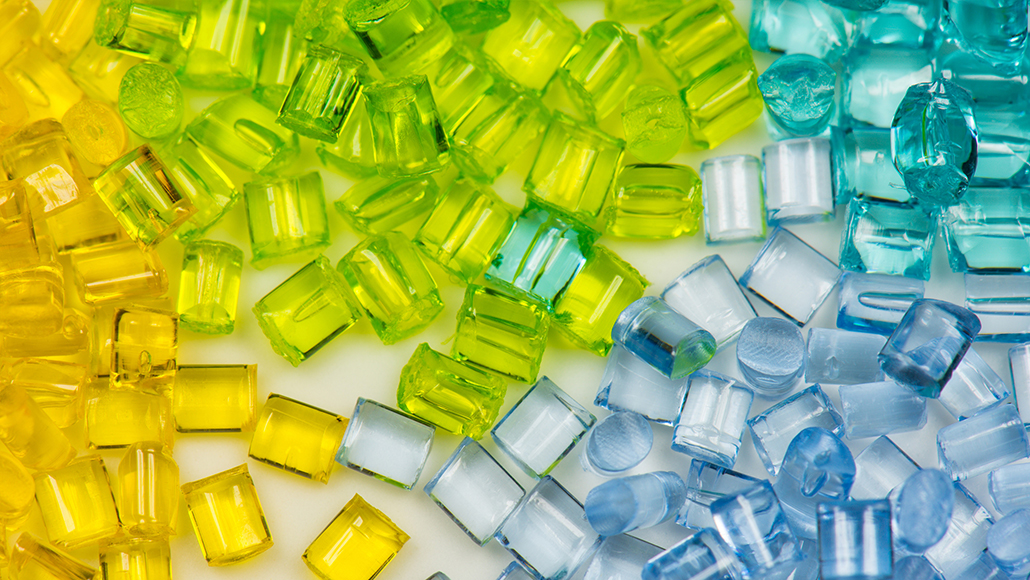
New Report Shows Tremendous Value to be Captured…. When We Stop Throwing Plastics in the Trash
The U.S. and Canada send over 34 million tons of plastics to landfills or incinerators each year. Following current trends, global plastics demand is forecasted to triple by 2050. And even more troubling, mismanaged waste leaks into our environment – there may be more plastics than fish (by weight) in our oceans by 2050.
But what if we could change that? What if we could use innovative chemical recycling technologies to purify, decompose, or convert waste plastics into the building blocks for renewed raw materials instead of discarding them after one use?
What if we could also reduce the world’s reliance on fossil fuel extraction, reduce landfill disposal costs for municipalities, decrease marine pollution, and generate billions in new revenue?
We can.
Investors and brands have an opportunity to influence and accelerate transformational technology solutions that repurpose plastics waste and keep materials in play in circular supply chains.
There are at least 60 technology providers developing these transformational technologies that purify, decompose, or convert waste plastics into renewed raw materials. This report proposes accessible, shared language to use to define and talk about each of these processes going forward:
Purification involves dissolving plastic in a solvent, then separating and purifying the mixture to extract additives and dyes to ultimately obtain a “purified” plastic. Purification processes make it possible to safely transform carpet into yogurt cups — greatly increasing the value of plastics waste. PureCycle Technologies will do just that when it opens its Ohio facility in the next year.
Decomposition is a process that involves breaking molecular bonds of the plastic to recover the simple molecules (“monomers” or “intermediates”) from which the plastic is made. In other words, plastic doesn’t just have to go back to plastic – it can become a valuable raw material to be used again. Loop Industries decomposes PET into its monomers and, with its partners, aims to produce a Loop-branded recycled PET pellet.
Conversion is similar to decomposition in that the process involves breaking the molecular bonds of the plastic. A key difference is that the output products from conversion processes are often liquid or gaseous hydrocarbons similar to the products derived from petroleum refining. These raw materials may enter different supply chains, such as fuels for combustion, and/or petrochemicals that can be made into intermediates and monomers for new plastics. Agilyx, based in Oregon, uses both decomposition and conversion technologies that can produce a variety of products, including naphtha, jet fuel, synthetic crude oil and styrene monomer, depending on the feedstock.
Through these technologies, it’s possible to recycle plastic back into plastic, AND to create valuable upstream products that keep materials in play.
The technology is possible. The question now is: How fast and how far can we go?
Every sector of society is engaged in the broad challenges of climate change and the visible problem of plastics waste. Many of the world’s largest and most influential brands are taking ownership of the problem and looking at their own supply chains. The Center for the Circular Economy at Closed Loop Partners is creating a roadmap for how to build on this momentum by unifying the diverse actors in this space and accelerating collaborative investment to bring solutions to scale.
Demand for plastics is strong and growing, yet the supply of recycled plastics available to meet demand is stuck at 6%. Options for recycling plastics today don’t capture the full opportunity: with current infrastructure, a small portion – less than 10% – of plastics waste from many consumer packages and products is recovered and recycled. Current mechanical processes and infrastructure aren’t enough to support the publicly stated goals of many global brands who have committed to use more recycled plastics in their products and packaging, or to achieve the zero waste goals of our major cities.
We surveyed more than 60 technology providers – broadly categorized as using one (or more) of three processes described above – nearly all of them at least at the lab stage of maturity, with significant potential to grow and scale. More than 40 of these solution providers are operating commercial scale plants in the U.S. and Canada today, or have plans to do so within the next two years.
But of the technology providers surveyed, it has taken them 17 years on average to reach growth scale. That’s not fast enough. More investment is needed now to accelerate these solutions – to go from “possible” to “probable”.
That’s why we are calling on investors, brands, and industry to join us in: investing to bring solutions to scale; increasing awareness of how these technologies apply to different supply chains and waste streams, including adopting the shared language from this research; and collaborating on partnerships with technology providers.
If these technologies are understood more broadly – and are more widely adopted and scaled – tremendous economic value can be realized. According to our analysis, if these technologies can meet market demands for plastics and petrochemicals, they have a potential addressable market of $120 billion ($47 billion for polymers) in the U.S. and Canada alone.
We need to stop thinking of plastics as waste, and start treating it as a resource. Until we do this, we are taking tons of value – and throwing it in the trash.
We hope you will take the time to read the full report: “Accelerating Circular Supply Chains for Plastics”. You can also see the overview of our key findings and recommendations for next steps here.
Join us: If you are interested in participating in our ongoing research, convening, and investment in this area, we encourage you to introduce yourself to the Center for the Circular Economy: [email protected].
We look forward to working together to accelerate solutions to plastics waste and circular supply chains.
Closed Loop Partners Announces 12 Winners of the NextGen Cup Challenge to Reimagine the Future of the Fiber To-Go Cup
February 27, 2019
Starbucks, McDonald’s and other industry leaders partner in pre-competitive collaboration to push the boundaries of sustainable design and find innovative cup solutions
NEW YORK, Feb. 27, 2019 /PRNewswire/ — The NextGen Consortium, convened by Closed Loop Partners, announced today the winners of the NextGen Cup Challenge – an open-sourced, global innovation challenge to redesign the fiber to-go cup and create a widely recyclable and/or compostable cup.
After a rigorous four-month review process by an esteemed group of judges including NextGen Consortium business leaders, as well as experts in recycling, composting and packaging, the Challenge narrowed the nearly 500 submissions from over 50 countries down to 12 winners.
These 12 winning solutions — broadly categorized into innovative cup liners, new materials, and reusable cup service models — have the potential to turn the 250 billion fiber to-go cups used annually from waste into a valuable material in the recycling system.
“This is a notable milestone to achieve our aspiration of sustainable coffee, served sustainably which is a particular passion for our over 350,000 Starbucks partners,” said John Kelly, Senior Vice President of Global Public Affairs and Social Impact at Starbucks. “We’re a founding partner of the NextGen Consortium because we believe it will take the scale and influence of many global companies to make recyclable, compostable to-go cups an industry standard rather than the exception.”
Many of the largest players in the food and beverage industry have united within the NextGen Consortium, making it a unique pre-competitive collaboration. Starbucks and McDonald’s were early investors and founding partners of the NextGen Consortium, with The Coca-Cola Company, Yum! Brands, Nestlé and Wendy’s joining as supporting partners. The World Wildlife Fund acts as an advisory member of the Consortium, and OpenIDEO is an innovation partner. Collectively representing a significant portion of the cups market, these brands are not only demonstrating their commitment to ending cup waste and driving innovation in packaging, but also accelerating the paths to global scale.
“McDonald’s is proud to work with such an unprecedented number of brands to address the issue of fiber to-go cups,” said Marion Gross, Senior Vice President and Chief Supply Chain Officer, McDonald’s USA. “Collaboration is what we need to truly move the needle, amplify impact and bring solutions to scale quickly.”
The NextGen Challenge winner solutions are advancing the transition to a more circular economy where materials are continuously cycled and reliance on raw materials is reduced. “By working across the entire value chain and engaging key stakeholders, winners of the NextGen Cup Challenge are tackling a complex problem in a holistic way, sending valuable material back into the supply chain – benefiting people, the planet, and businesses,” said Erin Simon, Director, Sustainability R&D, World Wildlife Fund.
Up to six winners will enter the NextGen Circular Business Accelerator, where they’ll gain access to a network of experts, business and technical resources and testing opportunities to ensure these innovations can successfully scale to serve the needs of the industry and maintain the performance standards we know and trust.
The Challenge is just the first stage of the NextGen Consortium’s three-year effort. Next, the NextGen Circular Business Accelerator, with testing and piloting opportunities, will help solutions get onto the shelf. Further, the Consortium is working with suppliers, recyclers and composters to ensure that the winning solutions can get successfully recovered for the highest value. The Consortium will work together to support the needs of the recycling and composting system and identify ways to make it easy for consumers to choose the right bin.
“The level of interest we saw in the Challenge demonstrates a real appetite for long-lasting sustainable packaging solutions,” said Kate Daly, Executive Director of the Center for the Circular Economy at Closed Loop Partners. “This level of industry collaboration in support of the NextGen Cup Challenge is really exciting, and we look forward to building on this momentum to encourage more innovative solutions. Fully recoverable fiber to-go cups are just the beginning.”
For more information on the winners, the Challenge and the NextGen Consortium, visit www.nextgenconsortium.com.
The 12 Winners of the Challenge
Category One: Innovative Cup Liners
These companies are rethinking the polyethylene plastic liners in cups that can currently make to-go cups difficult to recycle.
- C.E.E.R. SCHISLER, France, creates a 100% paper cup that is home compostable and recyclable.
- Colombier Group, Netherlands, Finland, creates a recyclable and compostable barrier for paperboard cups.
- Footprint US, USA, creates cups, lids and straws that are fully formed fiber-based solutions, with an aqueous-based coating that is recyclable and compostable.
- Kotkamills Oy, Finland, creates plastic-free, recyclable and compostable cupstock material that can be processed into cups at existing cup making machines.
- PTT MCC Biochem Company Limited, Thailand, creates a coated paper cup that is recyclable and home compostable.
- Solenis LLC, USA, Belgium, creates a barrier coating that is recyclable and compostable.
- Sun Chemical Corporation, USA, creates inks and coatings that are recyclable and compostable.
- WestRock Corporation, USA, creates a recyclable and compostable paperboard solution to cups.
Category Two: New Materials
These companies are using cutting edge, plant-based materials in their cups so that they are compostable.
- Solublue Ltd., UK, creates plant-based, food grade and non-toxic products that biodegrade after use.
Category Three: Reusable Cup Service Models
The cups made by these companies aren’t single-use, they just keep cycling – remaining in service by harnessing the power of technology and design.
- CupClub, UK, operates a returnable cup ecosystem, providing a service for drinks. Think bike sharing, but for cups.
- reCup GmbH, Germany, operates a deposit system for reusable cups. Rent their cup and return it to any participating partner shop. No cleaning of the cup or carrying around required.
- Revolv, Indonesia, Hong Kong (China), operates a deposit-based platform for smart, reusable beverage packaging, connecting their cups–and third party products–to Internet of Things technologies.
About NextGen
Each year, an estimated 250 billion fiber to-go cups are distributed worldwide. Most of these are not recyclable or compostable. The NextGen Cup Consortium and Challenge launched in 2018 to bring together entrepreneurs, industry, and recyclers to identify and commercialize the next generation of recyclable and/or compostable cups. Closed Loop Partners, Starbucks, McDonald’s, The Coca-Cola Company, Yum! Brands, Nestlé and Wendy’s invite the industry to join this effort to identify a global solution to this shared challenge.
About Closed Loop Partners
Closed Loop Partners is an investment platform that invests in sustainable consumer goods, recycling and the development of the circular economy. Investors include many of the world’s largest consumer goods companies and family offices interested in investments that provide strong financial returns and tangible social impact. In 2018, Closed Loop Partners launched the Center for the Circular Economy, a New York City-based collaboration center for innovators to commercialize products, services and technologies that are leading the transition from a linear take, make, waste economy to a restorative one in which materials are shared, re-used, and continuously cycled. Learn more at www.closedlooppartners.com.
About McDonald’s
McDonald’s is the world’s leading global foodservice retailer with over 37,000 locations in over 100 countries. Over 90 percent of McDonald’s restaurants worldwide are owned and operated by independent local business men and women. This year McDonald’s announced a series of commitments demonstrating how it will use its Scale for Good to positively impact the planet and the communities it serves. You can read more about McDonald’s Scale for Good initiatives here.
About Starbucks
Since 1971, Starbucks Coffee Company has been committed to ethically sourcing and roasting high-quality arabica coffee. Today, with stores around the globe, the company is the premier roaster and retailer of specialty coffee in the world. Through our unwavering commitment to excellence and our guiding principles, we bring the unique Starbucks Experience to life for every customer through every cup. To share in the experience, please visit us in our stores or online at http://news.starbucks.com or www.starbucks.com.
Additional Quotes
“Solving the issue of plastic waste requires collaboration among many different stakeholders,” said Stefan Palzer, Nestlé Chief Technology Officer. “We are excited to join the NextGen Consortium and Cup Challenge as it brings together start-ups, industry partners and suppliers to find an industry wide, global packaging solution for sustainable to-go cups.”
“Yum! Brands would like to congratulate all of the Challenge winners for bringing forward incredible innovation that will help find food packaging solutions for our industry and beyond,” said Jon Hixson, VP Global Government Affairs and Sustainability, Yum! Brands. “The NextGen Consortium provides an amazing platform for collaboration and we look forward to seeing the continued progress that comes from the partnership to drive positive change in the value chain.”
“At Wendy’s, we know that our customers are increasingly aware of packaging waste and its impact on the environment,” said Liliana Esposito, Wendy’s Chief Communications Officer. “We embrace our role as being part of the solution, and one way we do that is to engage in partnerships that help us arrive at smart solutions, like our partnership with the NextGen Consortium. We congratulate the winners in this phase of the NextGen Cup Challenge, and look forward to seeing their ideas come to life and make a difference.”
“It’s encouraging to see such a diverse range of innovative solutions that represent milestones in the journey toward more comprehensive recyclability and compostability of cups across the board,” said Nina Goodrich, Executive Director, GreenBlue and the Sustainable Packaging Coalition. (Nina Goodrich is a judge for the NextGen Cup Challenge)
“It’s great to see the momentum behind the NextGen Cup Challenge coming from a number of large brands,” said Abe Minkara, Managing Director, Mark Cuban Companies. “Together with the innovative winning ideas, the combination is truly powerful. Scaling a sustainable solution to the to-go cup ecosystem becomes not only attainable but inevitable.” (Abe Minkara is a judge for the NextGen Cup Challenge)
“The winners of the NextGen Cup Challenge represent an inventive spectrum of creative chemistry, design and manufacturing technology demonstrating real progress toward the recyclability and compostability of post-consumer cups and containers,” said Scott Seydel, Board Chair and CEO, The Seydel Companies and Board Trustee of the Ellen MacArthur Foundation US. (Scott Seydel is a judge for the NextGen Cup Challenge)
Contact: [email protected]
SOURCE Closed Loop Partners